After two fatality free years, Kumba Iron Ore believes that Zero Harm is achievable, but the change in mindset needs to start at the top, with a relentless focus on managing catastrophic and fatal risks.
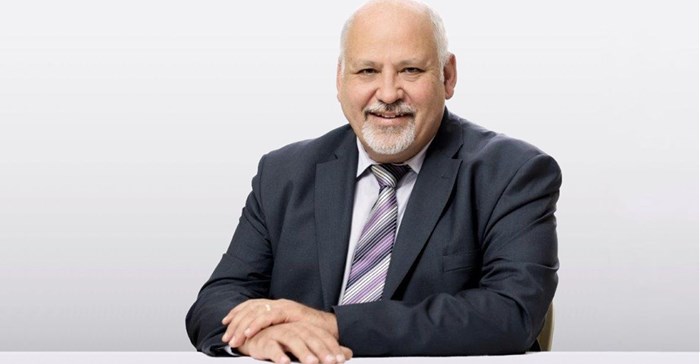
Philip Fourie, executive head of safety and sustainable development, Kumba Iron Ore
“By addressing the leading indicators for fatal accidents, they will be automatically eliminated. We know the fatal risks facing us, and we need to manage them properly,” said Philip Fourie, executive head of safety and sustainable development, Kumba Iron Ore.
Since it began implementing a comprehensive elimination of fatalities framework in the second half of 2016, Kumba has remained fatality free for almost two years. High potential incidents have reduced by 77% and total recordable cases by 45% for the first half of 2018.
Fourie says the elimination of fatalities approach recognises that fatality prevention and accident prevention are two different issues which demand a complete focus on managing fatal and catastrophic risk.
“The traditional thinking is that several lost time injuries (LTIs) turn into a fatality. That’s simply not the case. The circumstances that cause fatalities are totally different to those that cause accidents. If we had continued with the old approach of addressing the top five causes of accidents, we would have only prevented two of our 47 fatalities since 1972,” says Fourie.
Fourie outlined a six-point approach to achieving a zero-harm approach:
- it starts at the top. Leaders need to change their mindsets around safety and understand that whatever happens on their watch is a reflection of their leadership. At Kumba, safety results now form part of employee key performance indicators (KPIs), and as such, affect their performance-based remuneration.
- This is followed closely by creating a culture of safety and caring at the mines. This takes time and significant leadership commitment to establish. “To eliminate fatalities, leaders must be in the field where the risk work is taking place. When workers see this, they are encouraged to follow correct procedures more. This has had a major impact on reducing our accident rates,” said Fourie.
- It’s vital to implement a well-designed risk and change management process that identifies the critical controls of the fatal risks. Using benchmark figures, a typical opencast operation has in the vicinity of 800 controls to prevent accidents. "About 80 of these are critical controls, which can result in a fatal accident if they fail. “If we can ensure 100% compliance, 100% of the time, then we will eliminate fatal accidents,” says Fourie.
- Mines must become learning organisations. They need to learn properly from their own experiences, from the broader South African mining industry, and from the rest of the world.
- Proper planning and scheduling of fatal risk work is imperative – or, as Fourie says: “Unplanned work is unsafe work.”
- It’s vital to monitor safety performance and address shortcomings. Every high-potential hazard and incident has to be treated as if it was a fatal accident, with the same rigour and investigation processes.
“We truly believe that zero harm is achievable; this is supported by the fact that Kolomela mine achieved a record 154 injury-free days in 2017,” says Fourie. “But it’s an ongoing process. We can’t rest until we have 100% compliance.”